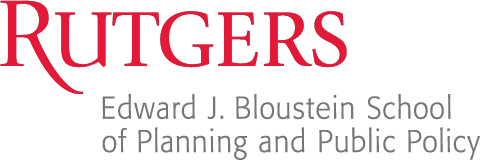
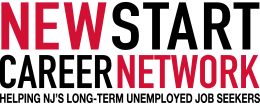
Job Information
J & J Truck Bodies and Trailers & J & J Truck Equipment Machine Operator in Somerset, Pennsylvania
Operates production machinery and hand tools to cut, fabricate position, align, and assemble parts. Reads and interprets blueprints, diagrams, and specifications and adjusts machine settings to produce parts and assemblies in a timely fashion and to an acceptable level of quality.
Essential Duties and Responsibilities include the following. Other job-related duties may be assigned in compliance with state and federal regulations.
· Locate and mark work piece bending and cutting lines, allowing for stock thickness, machine and welding shrinkage, and other component specifications.
· Measure completed workpieces to verify conformance to specifications, using micrometers, gauges, calipers, templates, or rulers.
· Study engineering drawings and blueprints to determine task sequences.
· Read work orders or production schedules to determine specifications, such as materials to be used, locations of cutting lines, or dimensions and tolerances.
· Set up, operate, or tend machines to saw, cut, shear, slit, punch, crimp, notch, bend, or straighten metal.
· Install, align, and lock specified punches, dies, cutting blades, or other fixtures in rams or beds of machines, using gauges, templates, feelers, shims, and hand tools.
· Move parts into position, manually or by using hoists or cranes.
· Set up and operate fabricating machines such as brakes, rolls, shears, flame cutters, grinders, and drill presses to bend, cut, form, punch, drill, or otherwise form and assemble metal components.
· Operate Computer Numerically Controlled (CNC) cutting equipment such as plasma, oxyfuel, laser, or water jet to perform profile cutting of aluminum and steel products.
· Starts and observes machine operation to detect malfunctions or out-of-tolerance machining and adjusts machine controls or control media as required.
· Verifies conformance of finished work piece to specifications.
· Confers with engineers, production personnel, programmers, or others to resolve machining or assembly problems.
· Perform duties in a safe manor; wear always required PPE.
· Observes and complies with all the provisions of the ISO 90001 QMS
Supervisory Responsibilities
This job has no supervisory responsibilities.
Competencies
To perform the job successfully, an individual should demonstrate the following competencies:
· Work within tolerance of +/- 1/16
· Meets productivity standards; Completes work in timely manner; Strives to increase productivity.
· Is consistently at work and on time.
· Demonstrates attention to detail.
· Strives to continuously build knowledge and skills.
· Open to others' ideas and tries new things.
· Balances team and individual responsibilities.
· Works within schedule, conserves organizational resources and uses time efficiently.
· Promotes a harassment-free environment & treats people with respect.
· Follows policies and procedures.
· Sets and achieves goals.
· Accepts responsibility for own actions; Follows through on commitments.
· Analytical - Synthesizes complex or diverse information; Collects and researches data; Uses intuition and experience to complement data.
· Designs workflows and procedures.
· Design - Applies design principles; Demonstrates attention to detail.
· Problem Solving - Identifies and resolves problems in a timely manner.
· Project Management - Completes projects on time and budget; Manages project team activities.
· Technical Skills - Strives to continuously build knowledge and skills, Shares expertise with others.
· Customer Service -Responds to requests for service and assistance; Meets commitments.
· Interpersonal Skills -Remains open to others' ideas and tries new things.
· Oral Communication - Listens and gets clarification; Responds well to questions; Demonstrates group presentation skills; Participates in meetings.
· Written Communication - Writes clearly and informatively; Varie writing style to meet needs; Presents numerical data effectively.
· Teamwork - Balances team and individual responsibilities.
· Change Management - Develops workable implementation plans; Communicates changes effectively.
· Delegation - Sets expectations and monitors delegated activities; Provides recognition for results.
· Leadership - Inspires and motivates others to perform well.
Managing People -Fosters quality focus in others; Improves processes, products, and services.
· Quality Management - Looks for ways to improve and promote quality.
· Cost Consciousness - Works within approved budget; Develops and implements cost saving measures; Conserves organizational resources.
· Diversity - Demonstrates knowledge of EEO policy; Shows respect and sensitivity for cultural differences; Promotes a harassment-free environment.
· Ethics - Treats people with respect; Works with integrity and ethically; Upholds organizational values.
· Organizational Support - Follows policies and procedures; Completes administrative tasks correctly and on time; Supports organization's goals and values.
· Strategic Thinking - Develops strategies to achieve organizational goals.
· Judgment - Exhibits sound and accurate judgment.
· Motivation - Sets and achieves challenging goals; Demonstrates persistence and overcomes obstacles.
· Planning/Organizing - Prioritizes and plans work activities; Uses time efficiently.
· Professionalism - Approaches others in a tactful manner; Follows through on commitments.
Quality - Actively supports the ISO 9001 QMS, contributes to its effectiveness, and instructs others in its purpose, use, and benefits.
· Quantity - Meets productivity standards; Completes work in timely manner.
· Safety and Security - Observes safety and security procedures; Determines appropriate action beyond guidelines; Uses equipment and materials properly.
· Adaptability -Able to deal with frequent change, delays, or unexpected events.
· Attendance/Punctuality - Is consistently at work and on time; Arrives at meetings and appointments on time.
· Dependability - Follows instructions, responds to management direction; Takes responsibility for own actions; Completes tasks on time or notifies appropriate person with an alternate plan.
· Initiative - Volunteers readily; Undertakes self-development activities; Seeks increased responsibilities.
Qualifications To perform this job successfully, an individual must be able to perform each essential duty satisfactorily. The requirements listed below are representative of the knowledge, skill, and/or ability
required. Reasonable accommodations may be made to enable individuals with disabilities to perform the essential functions.
Education and/or Experience
Vocational / technical training needed or a high school diploma or general education degree with work experience in an industrial manufacturing or paint shop setting.
Language Skills
Ability to rea