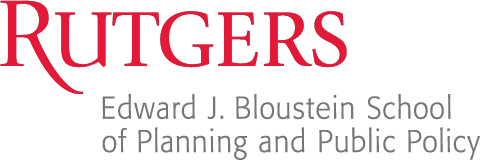
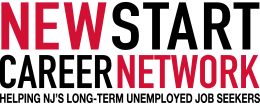
Job Information
Promotion In Motion Director, Technical and Maintenance Reliability in Somerset, New Jersey
Director, Technical and Maintenance Reliability
Job Details
Job Location
Somerset - Somerset, NJ
Description
JOB OVERVIEW
Primary responsibilities are to keep the manufacturing facility and all production processes mechanically operating at maximum rated capacity and producing quality products in a cost-effective manner across three shifts.
This role requires a master level Reliability practitioner who utilizes a broad knowledge base to provide direction in the development and implementation of tactical and strategic objectives.
This position will provide leadership to operational excellence program - including assessment and action plans to move from chaotic reactive to reliability centered maintenance model.
This role manages the technical & Reliability program progress and effectiveness in delivering improved reliability performance, building organizational capability and institutionalize.
The successful candidate will be accountable for the strategic development, deployment, and execution of the Operational Excellence program for Maintenance & Reliability; with the goal of transforming the PIM Brands asset performance to world class levels.
Involves the installation, repair, maintenance and troubleshooting of all machinery, tools and mechanical systems.
Ensures that maintenance of all equipment is completed and complies with customer specifications and ensures that food safety and quality are not jeopardized by complying with all GMP and HAACP Guidelines as well as SOPs.
Ensures maintenance of equipment complies with desired processing rates.
Manage process controls and automation of the plant.
DUTIES AND RESPONSIBILITIES
Manages the speed of repairs to minimize downtime, minimizes the use of labor and parts, removes glitches in start-up, and addresses problems pro-actively. Interfaces with plant management, shift supervisors, engineering, warehouse production and packaging supervisors and QA/QC personnel
Responsible for overseeing the maintenance, troubleshooting and repair, and calibration of electrical, electronic, mechanical, hydraulic and pneumatic equipment to include preventive and predictive maintenance.
Establish and execute the plant' s preventive and predictive maintenance program, including equipment failure records, provide trend information and corrective action to Management Teams.
Prepare and maintain various reports and records using Computerized Maintenance Management System; verifying the completion of all maintenance work and provide historical information for future maintenance planning.
Recommend and implement continuous improvement programs, which maximize the efficiency of maintenance and machine work and reduce future maintenance requirements. Ensure these new methods are implemented through updating of maintenance procedures and training.
Confer with Managers and other personnel to implement operating procedures, resolve system malfunctions, and provide technical information.
Research and analyze equipment proposals, specifications, manuals, and other data to evaluate the feasibility, cost, and maintenance requirements of designs or applications.
Specify system components or direct modification of equipment to ensure conformance with engineering design and performance specifications.
Evolves and recruits’ talent to support 24/7 operation automation and controls.
Drives process controls specialized projects to enhance shop floor management.
Progresses and owns instrumentation and controls.
Supports and advances business intelligence tools.
Report food safety and quality issues to Plant management and SQFP.
Follow PIM Brands GMP rules.
Monitor fellow employees for adherence to GMP’s.
Conducts regular assessment of facility needs, improvements and repairs and routinely inspects operating machinery, equipment and supporting systems.
Maintains and repair machinery, equipment, systems, and mechanized vehicles.
Ensures production operations by setting work priorities, repair and maintenance schedules, and installation of machinery and equipment.
Provides 24/7 coverage and emergency response including equipment repair, situation, stabilization, and the mobilizing of resources as needed.
Directs staff on projects, tasks and assignments within cost and time budgets, and on schedule.
In coordination with the Plant Manager recommends CAPEX and repair maintenance items, in-house construction, fabrication, and outside contractor projects.
Provides staff training and development.
Evaluates work and performance.
Ensures safe work practices and ensures a safe work environment.
Oversees boiler operations, HVAC systems and related machinery.
Develops, implements, and maintains written policies and procedures.
Verifies and ensures the documentation of all repair records, preventive maintenance records and logs all filters and replacement parts.
Develops new tools and techniques to improve monitoring and performance of machinery, equipment, and maintenance staff.
Oversees and monitors the scheduling and safe use of all shop equipment, and that they are in good working order.
Purchases, stores, and issues all parts for equipment maintenance.
Collaborate with VP Manufacturing to optimize the site maintenance budgets, maintenance plans, long term equipment replacement plans and spare part sourcing strategies.
Maintains log of all maintenance orders
Ensures total custody of all maintenance parts in the shop, storeroom and when installed.
Resolves maintenance problems and issues by working closely with plant management, supervisors, and QA/QC
Completes maintenance operational requirements by scheduling and assigning staff, monitors and ensures performance for maximum efficiency and effectiveness and follows up on results and completed tasks.
Works closely with plant management and the production staff to ensure that production schedules and needs can be met because production machinery is operational.
Responsible for staff working in a safe manner and that workplace safety issues are addressed and corrected.
Thoroughly familiar with physical plant services
Attends and participates in production meetings.
Monitors and minimizes down time, identifies and advocates for improvement opportunities.
Various projects as assigned by upper management.
Ability to work additional hours as needed.
PHYSICAL DEMANDS/ ESSENTIAL JOB FUNCTIONS
Standing, walking, sitting, bending, reaching, kneeling, and crouching. Manual dexterity of hands and fingers to handle or feel objects, tools, and controls. Must be able to read mechanical drawings, blueprints and charts Lifting and moving of objects weighing at least 50 lbs. Reasonable accommodations will be evaluated and considered to enable an individual to perform the essential job functions.
WORK ENVIRONMENT
Busy, active and noisy environment typical of a manufacturing operation. Work areas have a wide range of climates and temperatures. Work areas may contain by-products of manufacturing. The plant floor may be crowded and motorized product transport vehicles move throughout the plant Hair net, beard net, assigned work uniform, protective eye wear and gloves are among the GMP required apparel that must be worn, if indicated, on the plant floor.
WORK ENVIRONMENT
Busy, active and noisy environment typical of a manufacturing operation. Work areas have a wide range of climates and temperatures. Work areas may contain by-products of manufacturing. The plant floor may be crowded and motorized product transport vehicles move throughout the plant Hair net, beard net, assigned work uniform, protective eye wear and gloves are among the GMP required apparel that must be worn, if indicated, on the plant floor.
PIM Brands is an Equal Opportunity Employer. PIM Brands is an E-Verify Employer
#SOM123
#LI-NP1
Qualifications
EDUCATION, EXPERIENCE AND TRAINING
High School Diploma or GED is strongly preferred.
Technical and vocational education preferred.
Minimum 10 years mechanical experience in a manufacturing environment plus 7 years with supervisory or management responsibilities
Experience with automation, industrial controls and business intelligence tools.
Technical working knowledge in operation and maintenance of facility management services, steam generators, refrigeration, air conditioning, generators, blueprint reading and equipment maintenance
Must possess knowledge of OSHA requirements.
Must have knowledge of plc, motor controls and pump rebuilding. knowledge of Confined Space/Lock-Out Tag-Out requirements
Must be computer literate with office, technical and parts and maintenance software packages.
Must have well developed problem-solving skills and ability to develop conceptual alternatives.
Must have the ability to plan, organize, develop, implement and interpret programs, goals, objectives, policies and procedures in a food manufacturing environment.
PIM Brands is an Equal Opportunity Employer. PIM Brands is an E-Verify employer.