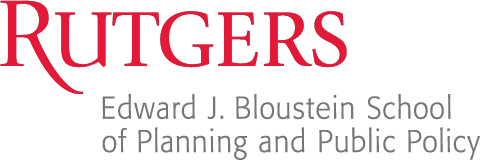
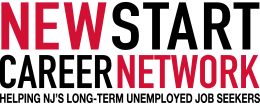
Job Information
LiDestri EHS (Environmental, Health & Safety) Manager- manufacturing in Rochester, New York
About LiDestri Food and Drink
LiDestri Food and Drink has grown from our roots as a pasta sauce and salsa manufacturer to become an R&D engine, formulating and producing innovative food products for our national and retailer brand partners. A family-run company based in Rochester, NY, LiDestri employs over 1,000 people across three U.S. locations. We have decades-long partnerships with some of the most respected consumer packaged goods (CPG) companies and the most highly inventive retailer brands.
Excellent Pay and Benefits:
Great career-pathing
Professional development, including unlimited online training courses
Health insurance with premium contributions
Dental, vision, HSA
100% company paid life insurance and long-term disability
401k – with employer match
Paid time off to include- vacation, sick pay, wellness time off, and 10 holidays
Company bonuses
And many more….
POSITION SUMMARY:
This position is responsible for actively developing, organizing, administering, and maintaining the safety, environmental, security programs and training for LiDestri Foods & Beverage in Rochester, NY. in conjunction with corporate direction. The purpose is to develop and maintain a safety culture that will minimize the number and reduce the severity of accidents and injuries. The EHS Manager will drive employee engagement in conjunction with management, while maintaining efficiency and the well-being of employees. The EHS manager must comply with all federal, state, and local regulations, and all corporate and division policies and procedures.
DUTIES & RESPONSIBILITIES:
Act as the primary authority in all areas of occupational safety, industrial hygiene, environmental compliance, and plant security for the facility
Participate as part of a corporate team to initiate, develop, and maintain policies and procedures that address key safety issues and concerns, including PPE’s, lockout/tag out, confined space, etc.
Develop and maintain policies and resources for site security. This will also include investigations when required
Execute and support corporate safety directives
Assist with determining corrective behavior for potential safety problems by reviewing formal reports from supervisory and management personnel and collaborating to determine solutions and prevention of future accidents and incident
Review work practices to make sure safety-related policies and procedures are being followed by employees and enforced by management
Notify supervisor and HR Manager of any policy or procedure violations, to determine corrective discipline
Ensure a proactive approach to accident prevention by training and advising management and employees on all safety issues
Effectively communicate safety related issues through management safety bulletins, safety newsletters, memos, and meetings
Maintain expertise on current safety issues through ongoing literature and attendance at relevant seminars and meetings
Work jointly and collaboratively with operations to improve operational efficiencies and improve health and safety costs
Assist with follow up on work restrictions
Coach, mentor and develop staff, including preparing and conducting employee performance appraisal
Maintain employee work schedules including timecard approval, work assignments, job rotation, training, vacations and paid time off
Organize required training in all departments to increase safety awareness and adherence
REQUIRED EDUCATION, SKILLS & EXPERIENCE:
High School diploma required, Associates degree required or Bachelor’s degree preferred in Environmental Health & Safety or equivalent experience and education
Minimum of two (2) years EHS management experience in manufacturing - preferably food or beverage industry
Demonstrated Technical Competencies - NIOSH, NY-OSHA, NFPA, NEC, Confined Space, LOTO, II&PP, Chemical/Physical hazards, Pesticides, Contractor Rules, Agricultural Rules, Heat Stress
Working knowledge of safety codes, NY-OSHA, Fed OSHA, Local Ordinances, Safety Best Practices, Emergency Response, First Aid, Industrial trucks/lifts, Training, OSHA site inspections and other regulatory agencies
Functional understanding or above of NFPA 13 and property exposure
501 certifications through OSHA preferred
Must have working knowledge of Microsoft Word and Excel
Must have high analytical aptitude and ability to work in a fast-paced environment
Strong interpersonal, communication (written and oral) and team-based skills are essential
Must be able to work across departments and build relationships with other departments to drive continuous improvement
Strong Project Management capability and experience.
WORKING CONDITIONS:
Time split between Plant (production floor) and Office environments
Required to wear personal protective equipment, as needed/required
Constant exposure to hot/cold weather and non-weather-related environment
Environment/work areas can be very wet, slippery and they have continuous forklift traffic
Will handle and work around various moving equipment and chemicals
Frequent lifting objects < 30 lbs. and pushing/pulling of objects less than 80 lbs. on carts
Long-term standing, constantly moving around on foot, frequent bending, and constant climbing of stairs
Must have the ability to go to all areas where product is in and test where testing equipment is located
DISCLAIMER: The duties listed above are intended only as illustrations of the various types of work that may be performed and is not an inclusive summary of job duties and responsibilities. The omission of specific statements of duties or responsibilities does not exclude them from the position. This job description does not constitute an employment agreement between the employer and the employee and is subject to change by the Company as the needs of the Company and requirements of the job change.
#IND