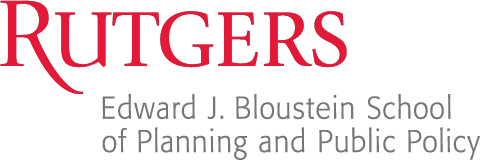
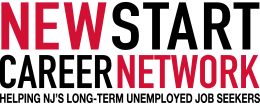
Job Information
Carlisle Interconnect Technologies Engineering Technician in Pottstown, Pennsylvania
SUMMARY
The Engineering Technician I perform engineering activities required to support, monitor, troubleshoot, and improve manufacturing processes and products. The engineering technician will provide technical support for the manufacturing area to which they are assigned (cable, assembly, plating, etc.).
ESSENTIAL JOB FUNCTIONS
- Provide technical support and oversight to production to meet quality, cost, and on-time delivery goals.
- Resolve production issues using root cause analysis and establishing corrective actions.
- Builds, tests, and evaluates engineering samples and prototypes.
- Utilizes lean manufacturing tools to improve quality and reduce waste (Standard work, 5S, Flow, Kanban systems, etc.)
- Participate in continuous improvement activities related to production processes.
- Participate in sustaining engineering activities (process and router updates).
- Oversee R&D production runs to validate new manufacturing processes.
- May perform technical training for specific tasks and require associated certifications (ex., J-STD-001, etc.)
- Develops/maintains/updates Work instructions and other related documentation.
- Performs advanced electrical, mechanical, and environmental testing to qualify and validate product performance.
Other duties as required in support of the department and the company
SUPERVISOR RESPONSIBILITIES
The responsibilities of this role do not include supervising other employees.
QUALIFICATIONS
To succeed in this job, an individual must satisfactorily perform each essential job function. The requirements below represent the required knowledge, skill, and ability. Reasonable accommodations may be made to enable individuals with disabilities to perform essential functions.
EDUCATION and EXPERIENCE
A high school diploma or equivalent, e.g., vocational school.
1+ years of experience manufacturing or testing microwave cables or related products/processes or an associate degree in Electronic Technology or a similar discipline with less than 1 year of experience.
Manufacturing experience in a custom make-to-order environment.
- Formal Problem-Solving Training (RCA, PDCA, 8D, etc.) preferred.
CERTIFICATES, LICENSES, REGISTRATIONS
- Active IPC-WHMA-A-620 certification at the manager's discretion and may be specific to work location.
LANGUAGE REQUIREMENTS
- Excellent verbal and written communication skills in English.
- Conversational in any other language preferred.
MATHEMATICAL SKILLS
- Interpret and analyze numerical data using statistical methods.
JOB SKILLS
- Basic understanding of MS Office Suite and SharePoint.
- Knowledge of ERP systems, SAP preferred.
- Practical knowledge of machines, production plants, and sites.
- Understand equipment, systems, and processes.
- Learn many skills on the job.
- Accurate documentation and adherence to specifications are essential.
- Working closely with engineers and other team members.
- Identifying and resolving issues efficiently.
- Understanding and experience in a Lean manufacturing environment.
- Participate in continuous improvement projects and 5S-related performance teams.
PHYSICAL DEMANDS
As part of their job duties, the employee must be able to sit, stand, and walk throughout the day while frequently using their hands to handle objects and communicate verbally. Additionally, they may need to reach, stretch, push, pull, crouch, stoop, and occasionally lift objects weighing up to fifty (50) pounds. This role requires specific vision abilities, including close, distance, color, peripheral vision, depth perception, and the ability to adjust focus. According to ADA regulations, reasonable accommodation will be provided to ensure that individuals with disabilities can perform the job's essential functions.
WORK ENVIRONMENT
A work environment in a manufacturing plant is the physical and social setting where goods production occurs. Depending on the type of p oduct, process, and plant, the work environment may vary in terms of noise, temperature, safety, and demand. Common characteristics of a work environment in a manufacturing plant are the use of machinery and exposure to hazards such as chemicals, heat, dust, or noise, with a culture of teamwork, communication, and continuous improvement.
ENVIRONMENTAL POLICY
Carlisle Interconnect Technologies is fully committed to minimizing the environmental impact of its operations, activities, and products. To achieve this, we adhere to all applicable environmental regulations and laws, prevent pollution, and continuously improve our environmental performance in all our global operations. This is possible through an Environmental Management System that provides a framework for setting and reviewing our environmental objectives and targets. We aim to identify and reduce any negative environmental impact our business activities may have.
PERSONAL PROTECTIVE EQUIPMENT REQUIREMENTS
- ASTM F-2412-2005, ANSI Z41-1999, or ANSI Z41-1991 rated safety toe shoes in specific areas.
- Clear ANSI Z87.1 safety-rated glasses in specific areas.
- Hearing protection in specific locations.
- Ability to compile with JSA in specific areas.
EXPORT COMPLIANCE DISCLAIMER
This position includes access or potential access to ITAR and EAR (Export Administration Regulations) technical data. Therefore, candidates must qualify as US Persons, defined as US Citizens or Permanent Residents (Green Card Holders).
TRAVEL
Approximately 10% of travel is expected.
SALARY INFORMATION:
According to several states' laws, this position's salary range falls between $22.12 and $26.55 hourly/annually. However, this salary information is merely a general guideline. When extending an offer, Carlisle Interconnect Technologies considers various factors such as the position's responsibilities, scope of work, candidate's work experience, education/training, essential skills, internal pay equity, and market considerations.
Equal Opportunity Employer Minorities/Women/Protected Veterans/Disabled