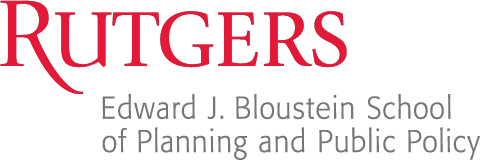
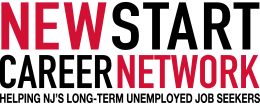
Job Information
Integra LifeSciences Sr Manufacturing Engineer in Plainsboro, New Jersey
Changing lives. Building Careers.
Joining us is a chance for you to do important work that creates change and shapes the future of healthcare. Thinking differently is what we do best. To us, change equals opportunity. Every day, more than 4,000 of us are challenging what’s possible and making headway to help improve outcomes.
SUMMARY
The Senior Manufacturing Engineer will play a key role in driving manufacturing excellence, process improvement, and ensuring the highest quality standards in production operations. They will collaborate with cross-functional teams, including R&D, Quality Assurance, and Operations, to optimize manufacturing processes, troubleshoot technical issues, conduct root cause investigations, and implement corrective and preventive actions (CAPAs). Their expertise will contribute to the successful delivery of safe, effective, and reliable medical devices that comply with regulatory requirements.
ESSENTIAL DUTIES AND RESPONSIBILITIES
Manufacturing Process Optimization: Lead efforts to optimize manufacturing processes, including equipment selection, process flow, capacity planning, and cycle time reduction to maximize efficiency and productivity.
Process Validation and Documentation: Develop and execute validation protocols (IQ, OQ, PQ) for manufacturing processes, ensuring compliance with regulatory standards. Coordinate specific efforts as required by the project team, including development of manufacturing process requirements, specifications, standard operating procedures (SOPs), Engineering studies, Engineering Change Orders (ECO) and Engineering Drawings.
Lead technical teams for identified projects and products, which may include personnel from Engineering, Manufacturing, Product Development, Marketing, QA, and Regulatory Affairs.
Continuous Improvement: Identify opportunities for process improvement and cost reduction through the application of Lean methodologies. Drive initiatives to enhance product quality, yield, and reliability.
Provide manufacturing input and support for the successful transfer of new products and processes into production.
Statistical process control: analyze and trend existing process parameters, process inputs and outputs to improve manufacturing yields, reduce manufacturing scrap, and error proof manufacturing processes.
Root Cause Investigations: Conduct thorough investigations into nonconformances and product failures to identify root causes. Utilize problem-solving techniques (e.g., 5 Whys, fishbone diagrams) to determine corrective actions and implement preventive measures.
Corrective and Preventive Actions (CAPAs): Lead the implementation and tracking of CAPAs. Ensure timely completion of CAPA activities, including root cause analysis, action plan development, implementation, and effectiveness verification.
Compliance and Quality Assurance: Ensure that all appropriate documentation, drawings, and specifications are generated in compliance with Integra’s procedures and statutory requirements (US FDA and ISO). Support internal and external audits to maintain compliance and address quality issues.
Training and Mentoring: Provide technical guidance and mentorship to junior engineers and manufacturing personnel.
Execute other work as assigned by management
DESIRED MINIMUM QUALIFICATIONS
Bachelor's degree in Engineering (Mechanical Engineering, Pharmaceutical Engineering, Chemical Engineering, Biomedical Engineering). Advanced degree is a plus.
5+ years of experience or 3+ years with Masters degree in engineering within the medical device industry.
Solid understanding of manufacturing processes, including batch processing, packaging, and sterilization.
Proficiency in process validation methodologies (IQ, OQ, PQ), statistical process control (SPC), and quality management systems.
Experience with Lean Manufacturing, Six Sigma, or other continuous improvement methodologies.
Ability to prepare complex technical reports, project summaries, and correspondence.
Familiarity with statistical tools (Minitab, Matlab, etc)
Excellent problem-solving skills with a data-driven approach.
Strong interpersonal and communication skills, with the ability to collaborate effectively across multidisciplinary teams.
Knowledge of regulatory requirements and standards applicable to medical device manufacturing.
Ability to manage multiple projects simultaneously and prioritize tasks effectively.
Excellent analytical thinking and technical writing skills
Demonstrates leadership in groups and teams
TOOLS AND EQUIPMENT USED
Typical office equipment (computer, phone, etc)
Lab equipment: Comfortable using engineering measurement devices: multi-meter, thermal mapping, data loggers, etc.
Manufacturing equipment: Lyophilizers, Autoclave, homogenizers, grinder, vacuum pump, pH meters, thermometers, balances (scales), water bath circulators, sonicators, humidity cabinet, mixers, centrifuge, blenders, air gun, drop indicator, Filamatic filling machines, slicer machines, scalpels, temperature recorders, Crosslinking chamber, humidification chamber, compression unit, cutting table, sealing machines, shrink wrap machines.
PHYSICAL REQUIREMENTS
Ability to view computer screen for extended periods
Must be able to stand and/or sit for extended periods of time
Must be able to move between manufacturing areas
While undertaking the essential duties and responsibilities of the position, the employee must repeatedly sit, listen, speak, and write/type. The employee must be able to stand for 8 hours, lift up to 60lbs and climb ladders without assistance. The employee is required to go to all areas of the company.
Ability to gown to ISO Class 5 type Clean Room standards and/or additional Clean room clothing.
Ability to gown to ISO Class 7 type Clean Room standards and/or additional Clean room clothing.
Ability to stand for 8 hours.
ADVERSE WORKING CONDITIONS
Open office work area with light to moderate noise
Able to work in a cleanroom/ controlled environment with gowning
Integra LifeSciences is an equal opportunity employer, and is committed to providing equal employment opportunities to all qualified applicants and employees regardless of race, marital status, color, religion, sex, age, national origin, sexual orientation, physical or mental disability, or protected veteran status.
This site is governed solely by applicable U.S. laws and governmental regulations. If you'd like more information on your rights under the law, please see the following notices:
EEO Is the Law (https://www.eeoc.gov/laws/index.cfm) | EOE including Disability/Protected Veterans (https://www.eeoc.gov/eeoc/publications/ada_veterans_employers.cfm)
Integra LifeSciences is committed to provide qualified applicants and employees who are disabled veterans or individuals with disabilities with needed reasonable accommodations in accordance with the ADA (https://www.eeoc.gov/eeoc/publications/fs-ada.cfm) . If you have difficulty using our online system due to a disability and need an accommodation, please email us at careers@integralife.com or call us at 855-936-2666.
Integra - Employer Branding from Integra LifeSciences on Vimeo (https://player.vimeo.com/video/265760526)