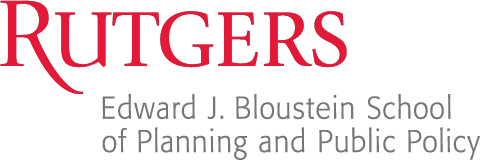
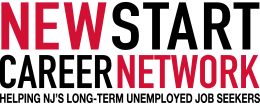
Job Information
Oshkosh Corporation Maintenance Technician in Bedford, Pennsylvania
About JLG, an Oshkosh company
JLG began in 1969, when our founder, John L. Grove set out to resolve growing safety concerns in the construction industry. Since then we have been committed to understanding the challenges and delivering innovative solutions to the access market. We partner with customers to provide quality equipment, training opportunities and trusted support within the access industry. We are a global company, and our products—including mobile elevating work platforms, telehandlers, utility vehicles and accessories—can be found all over the world.
Job Description
Maintenance Technician
Shift Times:
2nd Shift - 3pm-11pm
3rd Shift: 11pm-7
SUMMARY
Perform basic to intermediate equipment maintenance tasks and facility services with minimal supervision.
ESSENTIAL DUTIES AND RESPONSIBILITIES
• Perform scheduled and unplanned maintenance of all manufacturing equipment and buildings.
• Perform scheduled and unplanned maintenance of plant equipment including but not limited to CNC machine tools, manual machine tools, material handling equipment (including forklifts, agvs), paint equipment, automated inventory systems, power tools, hand tools, saws, presses, lifting devices, overhead cranes, exhausters, oxy-fuel, plasma cutting equipment, coolant systems, filtration systems, robots, welders and compressed air system
• Perform scheduled and unplanned maintenance of facility buildings and grounds, including but not limited to: HVAC systems, sprinkler systems, plumbing and sewer, lighting, gates, fencing, office furniture
• Troubleshoot, diagnose, rebuild and repair a wide variety of manufacturing equipment
• Record parts or materials used and order or requisition new parts or materials as necessary using electronic devices, such as iPads, iPhones and laptops.
• Support maintenance staff in moving and organizing production and office areas
• Provide support and assist with project work directed by the Maintenance Manager, Plant Manager and/or Supervisors
• Understand and follow all workplace safety rules, such as safe work practices and standard operating procedures.
• Maintain a safe and clean work environment in compliance with safety procedures, rules, and proper 6S standards
• Understand and follow all Personal Protective Equipment (PPE) requirements.
• Pick-up and delivery of maintenance repair and project parts; including coordination of ordered materials and logistics of payment
• Assisting contract workers throughout the site
• Regular attendance required
• Other duties as assigned
PREFERRED QUALIFICATIONS
• Experience in industrial, mechanical, electrical or moving vehicle maintenance
• Ability to operate forklifts, overhead cranes, man lifts, and power tools.
• Intermediate ability to troubleshoot and repair electrical, hydraulic, or mechanical problems on various manufacturing equipment including CNC equipment.
• Must be capable of reading and understanding electrical schematics and diagrams.
• Basic working knowledge of programmable ladder logic (PLC)
• Electrician skills including correct wiring practices, 3 phase electric power, replacement of electrical components including push buttons, breakers, motor starters and field sensors.
• Proficient with electrical test and diagnostic equipment (volt meters, ammeter, AC drives)
• Experience with Computerized Maintenance Management System (CMMS), such as Manager Plus, MaintainX, eMaint, Flix, Limble
WORKING CONDITIONS:
Physical Demands: Frequent: Standing, Walking, Reaching, Hearing, Talking, Visual; Occasional: Climbing, Sitting, Lifting/Carrying up to 35lbs., Pushing/Pulling up to 50lbs and up to 30lbs sustained.
Non-Physical Demands: Occasional: Analysis/Reasoning, Communication/Interpretation, Math/Mental Computation, Reading
Environmental Demands: Occasional: Frequent Task Changes, Tedious/Exacting Work, Dust, Temperature Extremes, Loud Noises. Frequent: working at heights, working indoor and outdoor, exposure to the weather
Work Schedule: Routine shift hours. frequent overtime
Oshkosh is committed to working with and offering reasonable accommodations to job applicants with disabilities. If you need assistance or an accommodation due to a disability for any part of the recruitment process, please contact our talent acquisition team at corporatetalentacquisition@oshkoshcorp.com .
Oshkosh Corporation is an Equal Opportunity and Affirmative Action Employer. This company will provide equal opportunity to all individuals without regard to race, color, religion, sex, sexual orientation, gender identity, national origin, disability, or veteran status. Information collected regarding categories as provided by law will in no way affect the decision regarding an employment application.
Oshkosh Corporation will not discharge or in any manner discriminate against employees or applicants because they have inquired about, discussed, or disclosed their own pay or the pay of another employee or applicant. However, employees who have access to the compensation information of other employees or applicants as a part of their essential job functions cannot disclose the pay of other employees or applicants to individuals who do not otherwise have access to compensation information, unless the disclosure is (a) in response to a formal complaint or charge, (b) in furtherance of an investigation, proceeding, hearing, or action, including an investigation conducted by the employer, or (c) consistent with Oshkosh Corporation's legal duty to furnish information.
Certain positions with Oshkosh Corporation require access to controlled goods and technologies subject to the International Traffic in Arms Regulations or the Export Administration Regulations. Applicants for these positions may need to be "U.S. Persons," as defined in these regulations. Generally, a "U.S. Person" is a U.S. citizen, lawful permanent resident, or an individual who has been admitted as a refugee or granted asylum.